9 Minute Read
How to Pour the Perfect Concrete Slab: A Comprehensive Guide
A solid foundation is crucial for the stability, longevity, and performance of your metal building or carport. Whether you’re installing a new garage, workshop, or storage space, a properly poured concrete slab provides the ideal base for your structure. This guide will walk you through the essential steps to create a durable concrete foundation that will support your metal building for decades to come.
To speak with a Carport Co. team member, call (888) 293-5588, email [email protected], or request a FREE estimate. You might also find our 3D Design Tool helpful for visualizing your future metal garage building.
Get Started
It’s quick and easy! Get a quote for an engineer stamped metal building today!

Manufactured in the United States

Competitive Warranties

Licensed and Insured Installers

Outstanding Customer Service
Structures That Stand Strong™
Table of Contents
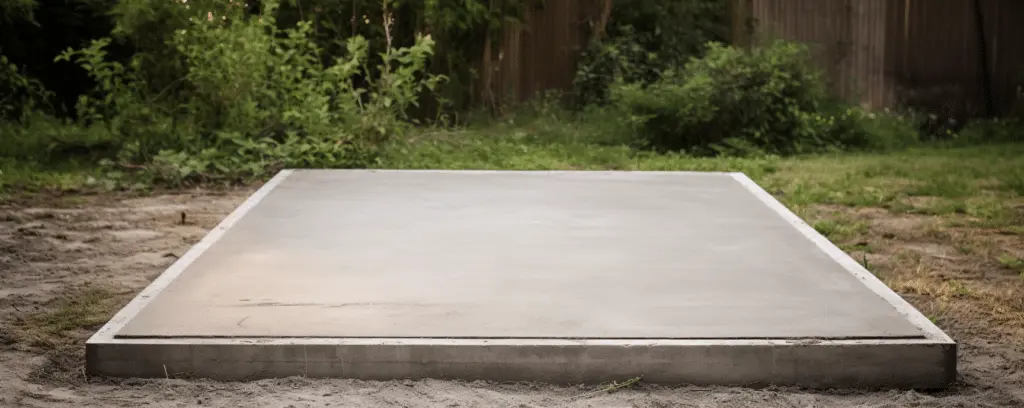
Understanding the Importance of a Proper Foundation
Metal buildings require level, stable foundations to ensure structural integrity. A well-constructed concrete slab:
- Prevents shifting and settling that could damage your metal structure
- Provides a clean, level floor surface
- Increases the lifespan of your metal building
- Improves drainage and moisture control
- Adds value to your property
Planning Your Concrete Slab
There is a lot that goes into pouring the perfect pad, and we’re here to help make understanding the process simple and easy to follow. When you planning your metal building’s concrete pad, you should:
1. Determine the Required Dimensions
In most areas, your concrete slab should extend 3-6 inches beyond your structure on all sides. For example, if you’ll be building a 24 f.t. x 30 f.t. metal garage, you should pour your pad 25 f.t. x 31 f.t. This gives ample room to provide a structurally sound foundation, while also avoiding water build up and pooling.
2. Calculate Concrete Needs
For most residential metal buildings and carports, a 4-inch thick slab is sufficient. For larger structures or those housing heavy equipment (such as 2 or 4 post lifts), consider a 6-inch slab or thicker. Use this formula to estimate the amount of concrete needed:
Length (ft) × Width (ft) × Thickness (ft) ÷ 27 = Cubic Yards of Concrete
3. Check Local Building Codes
Before beginning your project, it is essential you check with your local building department regarding:
- Permit requirements—Do You Need a Permit for a Metal Carport
- Setback restrictions
- Specific foundation requirements
- Frost line depths in your area
- Concrete requirements
Every city and township has varying requirements, and even though we can do our best to give you advice in this article, it could be incompatible with your town’s requirements, which is why we recommend to stop buy your building authority and run everything by them before starting your pour.
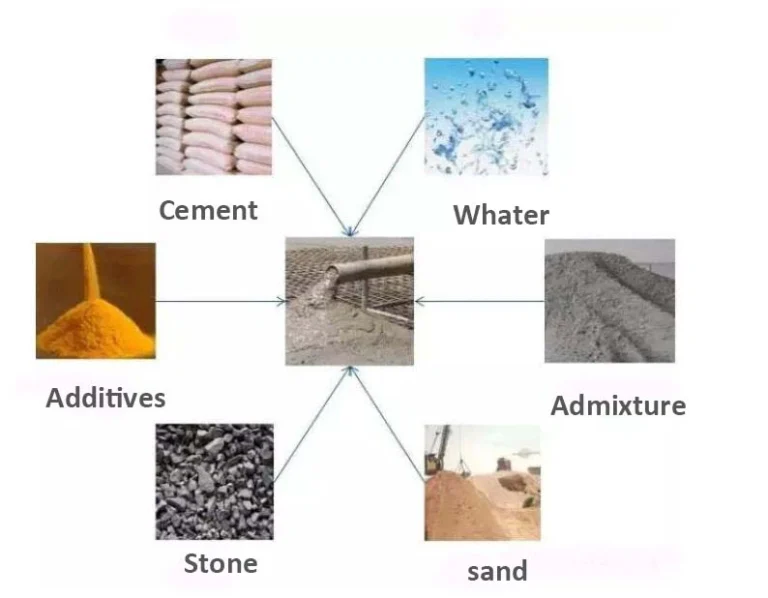
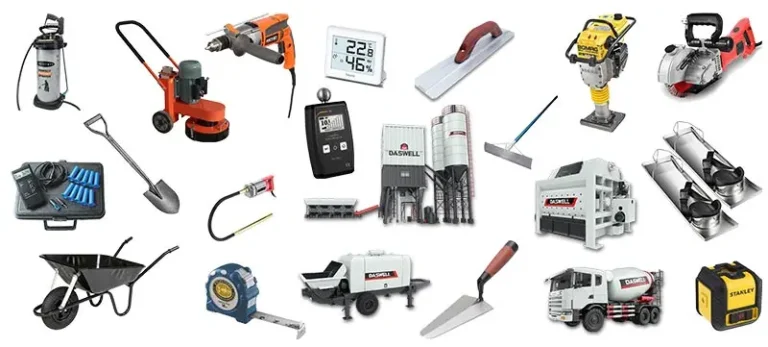
Materials and Tools Needed
We have included a list of tools and materials you’ll need when pouring your concrete pad. You can buy most tools and material on Amazon and have it shipped directly to your door.
Materials:
We would like to mention again that these are simply recommendations based upon prior experience. Always double check with your local building department what requirements they have for concrete slabs, as they vary wildly from city to city.
Tools:
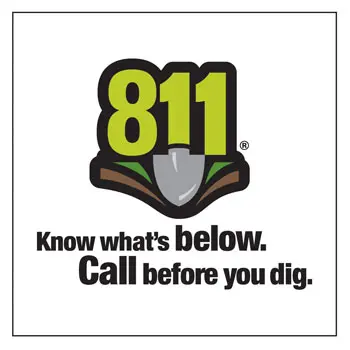
Step-by-Step Process for Pouring Your Concrete Slab
1. Site Preparation (1-2 days)
- Clear and level the area: Remove all vegetation, topsoil, rocks, and debris from the site.
- Mark the dimensions: Use stakes and string to outline the perimeter of your slab, ensuring square corners with the 3-4-5 method.
- Check for utilities: Always call 811 or your local utility locating service before digging.
- Excavate the area: Dig down approximately 8 inches (4 inches for gravel base and 4 inches for concrete).
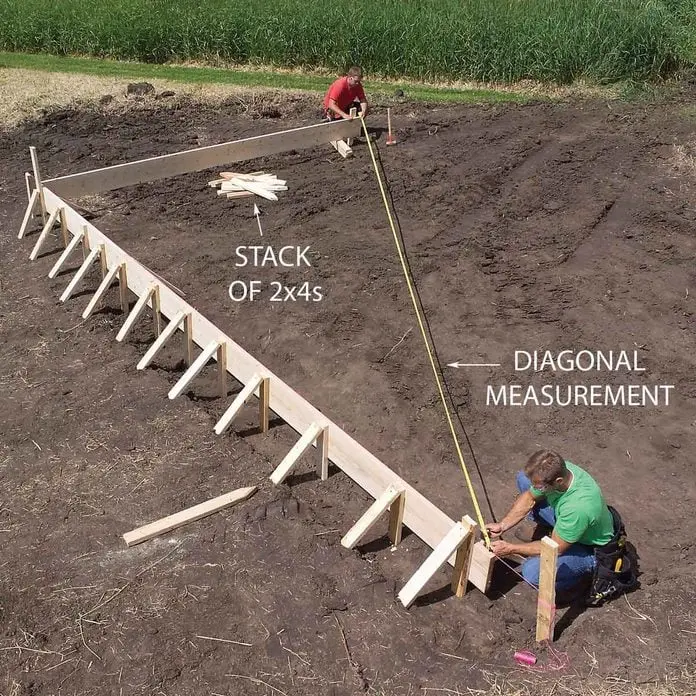
2. Build the Forms (1 day)
- Install wooden forms around the perimeter using 2×4 lumber.
- Secure forms with stakes placed every 2-3 feet.
- Check that forms are level and square.
- Apply form release agent to the inside of forms for easier removal later.
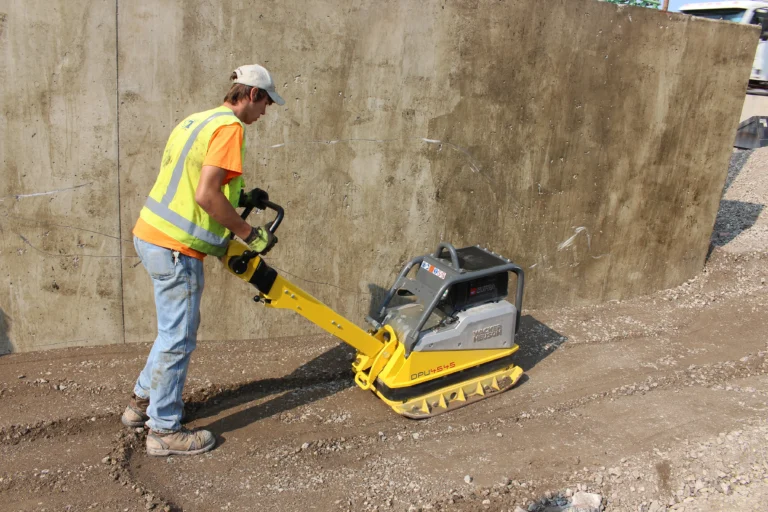
3. Prepare the Base (1 day)
- Add a 4-inch layer of gravel or crushed stone.
- Compact the gravel thoroughly using a plate compactor.
- Ensure the base is level across the entire area.

4. Add Reinforcement (1 day)
- Lay down the polyethylene vapor barrier over the compacted gravel.
- Install rebar in a grid pattern (typically 24 inches on center).
- Use rebar chairs to keep the reinforcement centered within the concrete.
- For additional strength, add wire mesh over the rebar grid.

5. Pour the Concrete (1 day)
- Choose a day with mild weather conditions (ideally 50-80°F).
- If using ready-mix concrete, coordinate delivery time with your preparation schedule.
- Pour concrete starting from one corner, working systematically across the area.
- Use a screed board (straight piece of lumber) to level the concrete to the top of the forms.
- Insert anchor bolts at marked locations before concrete begins to set.
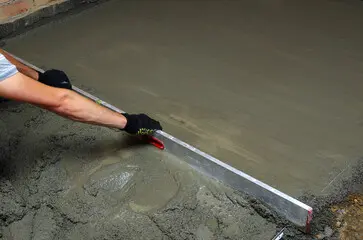
6. Finishing the Slab (Same day as pouring)
- Allow the concrete to set until water disappears from the surface (typically 1-3 hours).
- Use a bull float to smooth the surface.
- Use an edger tool to round the edges along the forms.
- For a non-slip surface, use a broom to create light texture across the slab.
- Consider adding control joints every 8-10 feet to manage cracking.
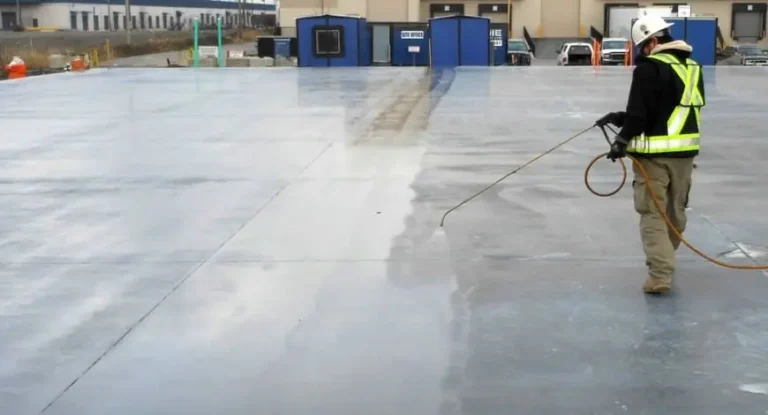
7. Curing the Concrete (7-28 days)
- Allow concrete to cure for at least 7 days before removing forms.
- Keep the surface moist for the first week by periodically spraying with water or covering with plastic sheeting.
- Apply concrete sealer after 28 days for additional protection.
- Wait at least 7 days before installing your metal building on the new slab.
Special Considerations for Metal Buildings
Drainage Planning
Ensure your slab has a slight slope (approximately 1/8 inch per foot) away from the center to promote water drainage. This prevents water pooling inside your metal building.
Thickened Edges
Consider creating thickened edges (8-12 inches) around the perimeter of your slab for additional support where the metal building will bear its weight.
Electrical and Plumbing Considerations
If your metal building will include utilities:
- Install conduit for electrical wiring before pouring concrete
- Place plumbing lines and drains in position
- Mark locations clearly to avoid damage during the pour
Cost Considerations
The total cost for a concrete slab foundation will vary based on:
- Size of the slab
- Thickness of the concrete
- Labor costs in your area
- Accessibility of the site
- Special requirements (reinforcement, finish type)
For a basic 24 f.t. × 30 f.t. slab (4 inches thick), expect material costs between $4,320-$5,760, with additional costs for professional installation if you’re not doing it yourself.
Professional vs DIY Considerations
While pouring a concrete slab is possible as a DIY project, consider these factors:
- Concrete work requires specific skills and experience
- Mistakes can be costly and difficult to correct
- Professional concrete contractors have specialized equipment
- Larger slabs (over 12′ × 12′) are challenging for beginners
- Professional installation often includes warranties
For most metal building installations, hiring a professional concrete contractor is recommended to ensure proper foundation support.
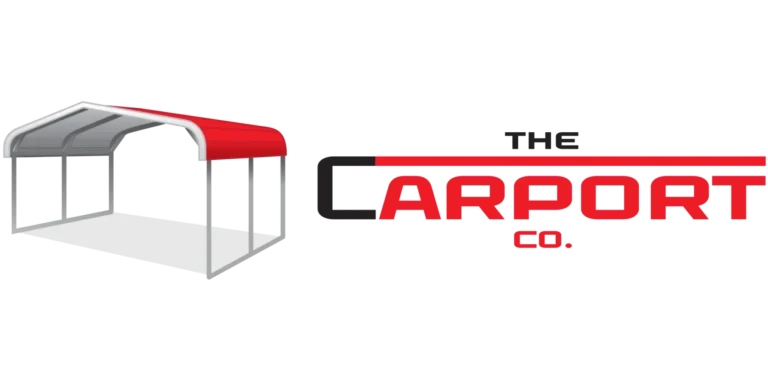
Ready to Work With The Carport Co. for Your Structure?
When you choose The Carport Co., you’re not just buying a steel carport or metal building—you’re getting a partner who’s committed to your satisfaction. Here’s what sets us apart:
Competitive Pricing: All of our pricing is either factory-direct, or less than factory direct through dealer exclusive sales and discounts.
Nationwide Coverage: We serve the majority of the United States, bringing durable carports to your doorstep (or driveway).
Premium Materials: Our metal buildings are made from prefabricated tube steel (galvanized steel), available in both 14-gauge and 12-gauge for added strength and durability.
Expert Guidance: Our team is here to help you every step of the way, from choosing the right structure to installation.
Frequently Asked Questions
How long does concrete need to cure before installing a metal building?
Concrete should cure for a minimum of 7 days before supporting any weight, but waiting 28 days allows the concrete to reach 90% of its full strength. Check with your metal building manufacturer for specific recommendations.
Do I need a permit to pour a concrete slab?
Most localities require permits for concrete slabs over a certain size. Always check with your local building department before beginning your project.
How thick should a concrete slab be for a metal garage?
For standard residential metal garages, a 4-inch thick slab is typically sufficient. For commercial applications or buildings housing heavy equipment, consider 6 inches with additional reinforcement.
Can I pour concrete directly on dirt?
No, pouring directly on dirt will lead to cracking and settling. Always prepare a proper base with compacted gravel and a vapor barrier.
How do I ensure my concrete slab is level
Use string lines, laser levels, and regularly check with a standard level during form construction and concrete pouring. The gravel base should be meticulously leveled before pouring.
What is the best time of year to pour a concrete slab?
Spring and fall typically offer ideal temperatures. Avoid extreme heat (above 90°F) which causes rapid drying, and never pour when temperatures might drop below freezing within 48 hours.
How much does a concrete slab for a metal building cost?
Expect to pay $4-$8 per square foot for materials and labor, depending on your location, slab thickness, and site conditions.
Can I add a concrete slab under my existing metal building?
While possible, it’s extremely challenging and not recommended. It’s typically more cost-effective to disassemble the building, pour the slab, and reassemble the structure.
How do I prevent cracks in my concrete slab?
Proper site preparation, adequate reinforcement, appropriate concrete mix, control joints, and proper curing techniques all help minimize cracking.
What type of finish is best for a metal building floor?
A light broom finish provides good traction while still being easy to clean, making it ideal for most metal building applications.
Table of Contents
Ready to Begin Your Project?
Do you think The Carport Co. would be a good fit for you? We’d love to earn your business. Fill out the quote form, and one of our friendly representatives will be in touch with you shortly. We’re here to answer questions you may have, provide personalized recommendations, and get you an estimate on your project.
To speak with someone, call (888) 293-5588 or email [email protected].
Don’t miss out on the opportunity to enhance your property with a durable, versatile, and visually appealing metal structure. Contact The Carport Co. today and experience what we can do.
Visit our 3D Builder to design your own structure!
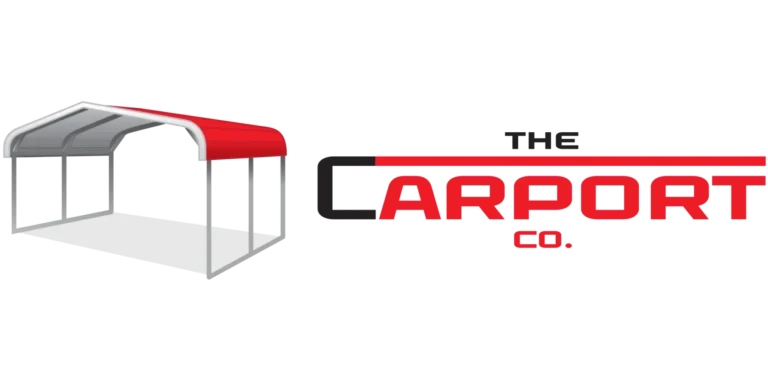
Get Your FREE Custom Quote
No-obligation, 100% FREE quote, delivered in minutes.
The Ultimate Buyer’s Guide is a collection of articles by The Carport Co. These articles have been catered to first time steel and metal carport, garage, and commercial building buyers. Our goal is to share as much information with customers as possible, to help make informed decisions, and ensure a customer doesn’t discover an addition they would have liked to added at the time of sale, but was not aware of the option’s existence.
Here is a preview of a few articles. To view the full Buyer’s Guide, please visit the Ultimate Buyer’s Guide page.